This old and dilapidated concrete floor slab has been re- laid and newly installed by the innovative concrete flooring contractors Level Best Concrete Flooring in Worcester on behalf of Hollis Global. The original floor was damaged with broken down joints … Read More
Joint Free Concrete Flooring
Joint Free Flooring (JFF)
Extending the Boundaries
A warehouse floor without a single joint
Level Best Concrete Flooring cast a completely seamless floor in one day. A
single panel of 42 × 18m wide – beyond Technical Report 34’s(1) aspect ratio
guidance for standard jointless slabs.
Level Best Concrete Flooring has constructed the first warehouse concrete floor slab in the UK using a system created using both steel fibre reinforcement in conjunction with steel post tensioned bars. The flooring system is not only joint free, but also crack free as the shrinkage is controlled using the hybrid reinforcement. This joint free floor slab was cast in one day with the industrial concrete flooring contractors utilising one of their light remote controlled laser screeds to reduce weight on the membrane during trafficking and concrete install. Although technically more complicated to construct than a more traditional warehouse concrete floor, Level Best managed to overcome any potential design and install problems using out of the box thinking and vast experience in floor slab technology. The joint free floor has many benefits to end users such as extremely low maintenance, easy to clean and keep hygienic, high surface abrasion resistance, high impact resistance and cost effective for the right uses. Not only has the floor slab no joints, but it also has no shrinkage related cracking, a unique scenario for concrete poured in mass during the summer months.
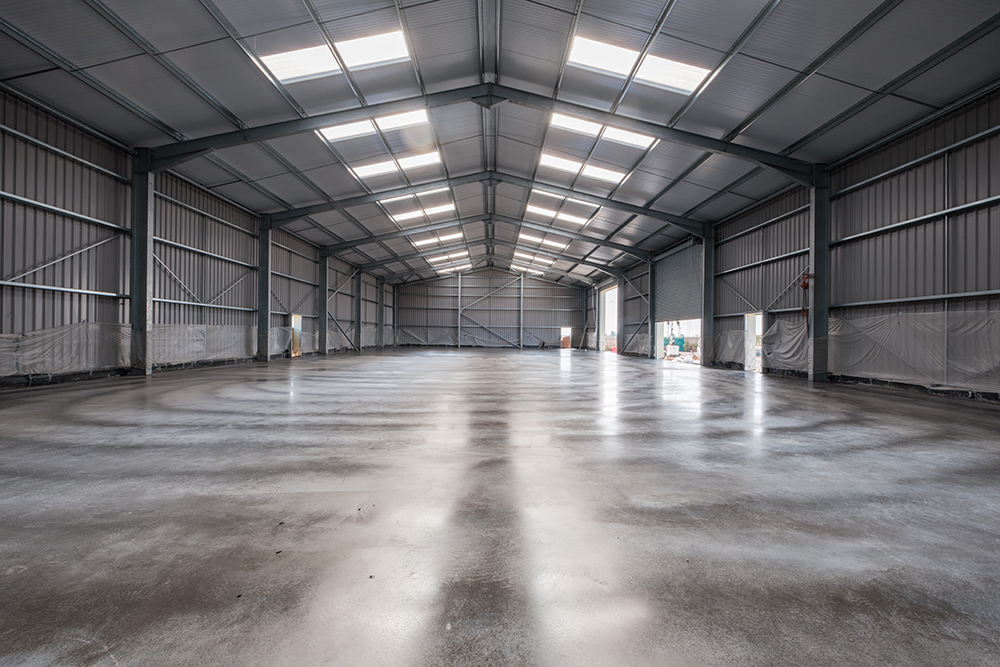
OUR SERVICES
- Design & Build
- Floor Renovation System (FRS)
- Industrial Concrete Flooring
- External Concrete Flooring
- Repairs, Removal & Replacement
- Industrial Concrete Cleaning
- Sub Base Levelling
- Joint Free Flooring (JFF)
Significant Benefits
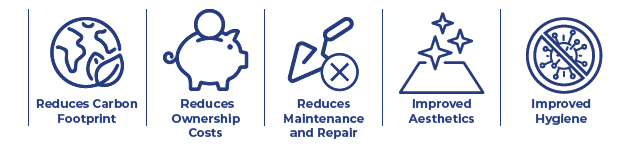
Compared with conventional reinforcement solutions, Joint Free Flooring reduced steel use in the building significantly; it was estimated that the overall carbon footprint of the seamless floor was reduced by 30% compared with a like-for-like conventional reinforcement system.
By creating joint-free distances up to 150m in some cases, Joint Free Flooring reduces the number of joints and associated weaknesses. Over time, this will diminish the maintenance and repair costs and increase floor durability.
The end result for Level Best Concrete Flooring was a floor with a low total cost of ownership, no joints and no reinforcement detailing, more spacious interiors, greater flexibility of layout and better aesthetics.
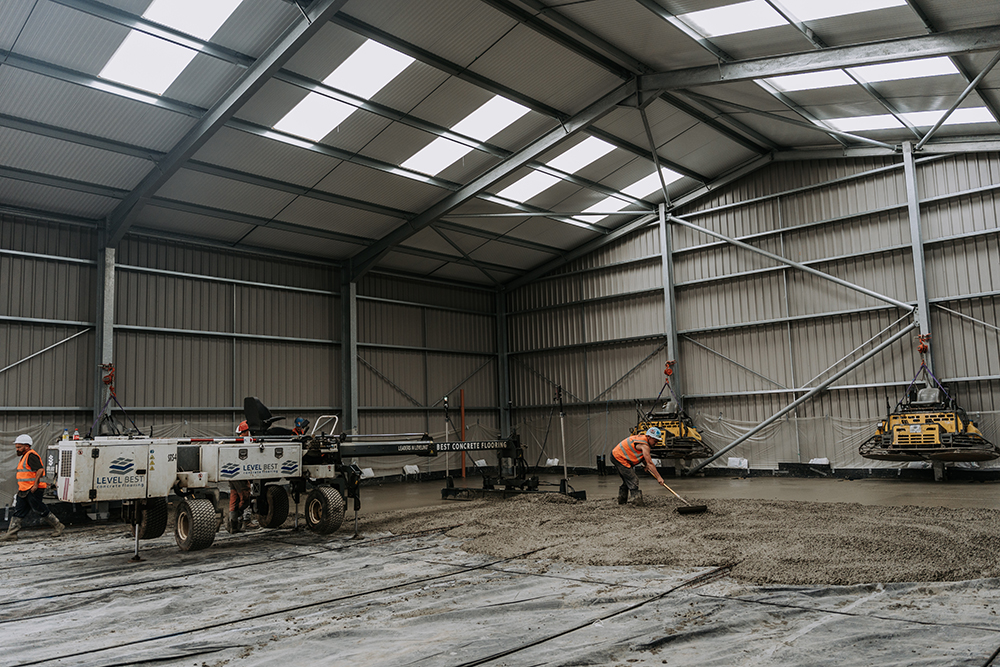
Three Step Process
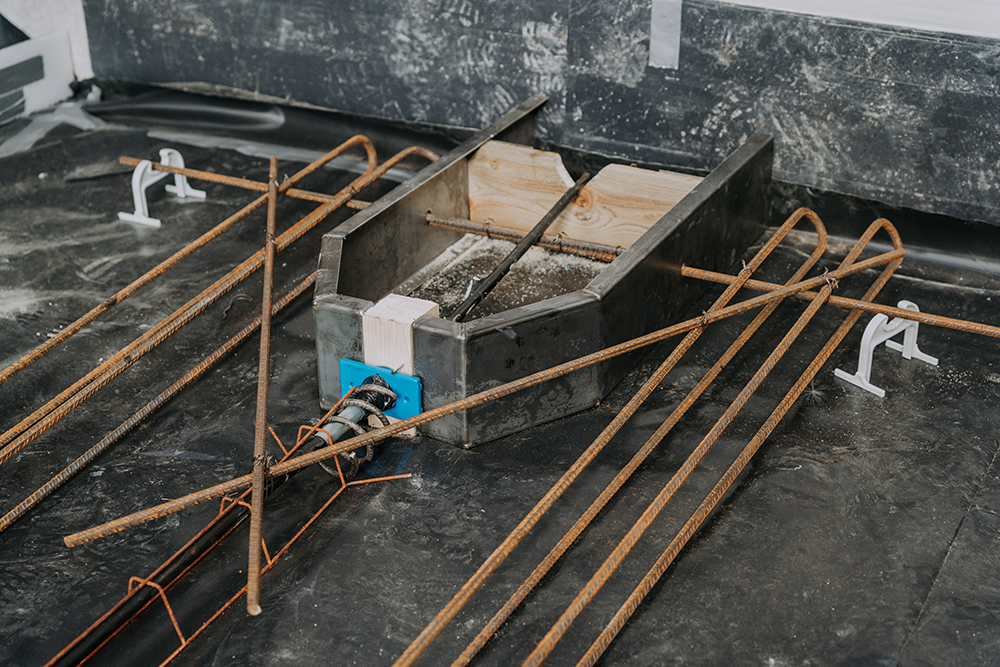
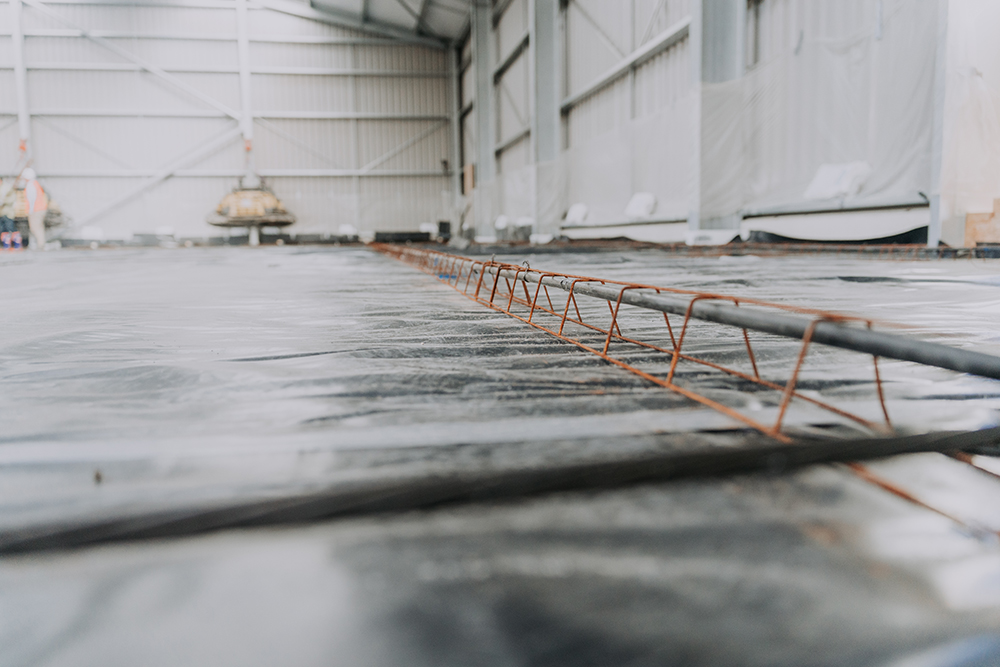
Step 1 - Preparation
Level Best Concrete Flooring ensured all subbase levelling was completed prior to the installation day. Prefabricated posttensioning tendons (pre-cut strands with anchors already fixed), which
allowed the post-tensioning to be installed in less than a day.
Due to restricted slab edge access and to avoid infill strips of floor area designated for the post-tensioning tendon stressing operation, pockets (similar to column isolation joints) were located at one end of the building, to allow future access of a stressing jack.
Due to the width of the building and the pour occurring in one single day, only longitudinal strands were required.
Step 2 - Concreting
Steel fibres were added to the concrete on site. The fibres are glued in bundles that are gradually released during mixing to disperse evenly through the concrete without balling. The steel fibre concrete was poured onto the ground by direct discharge from concrete trucks. The process for finishing the surface of the concrete slab to the required flatness and levelness was identical to typical flooring construction. Level Best also applied a dry shake topping to the surface of the concrete to increase toughness and abrasion resistance.
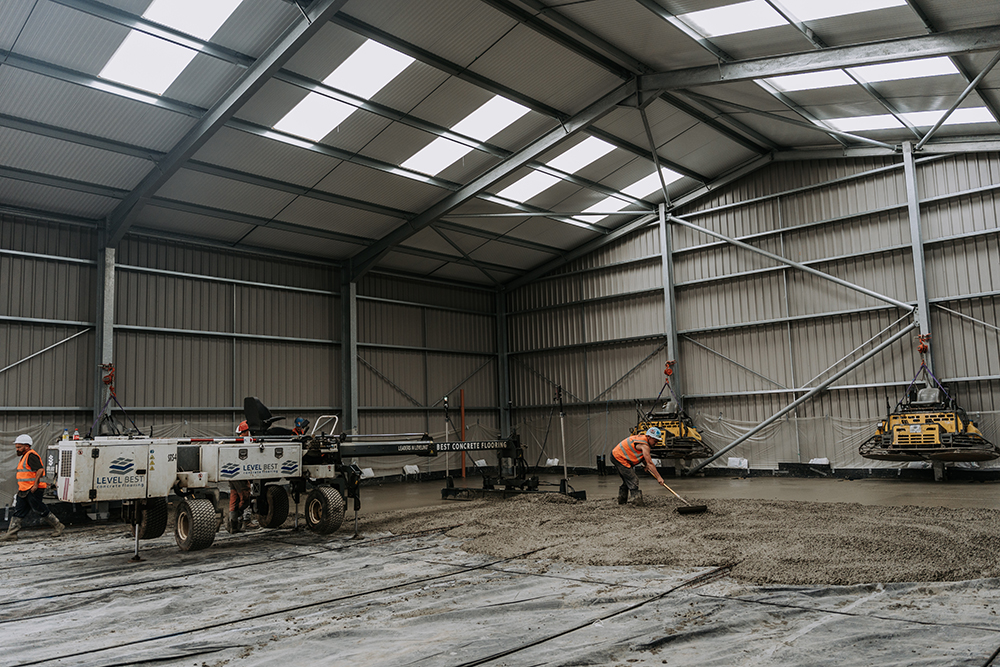
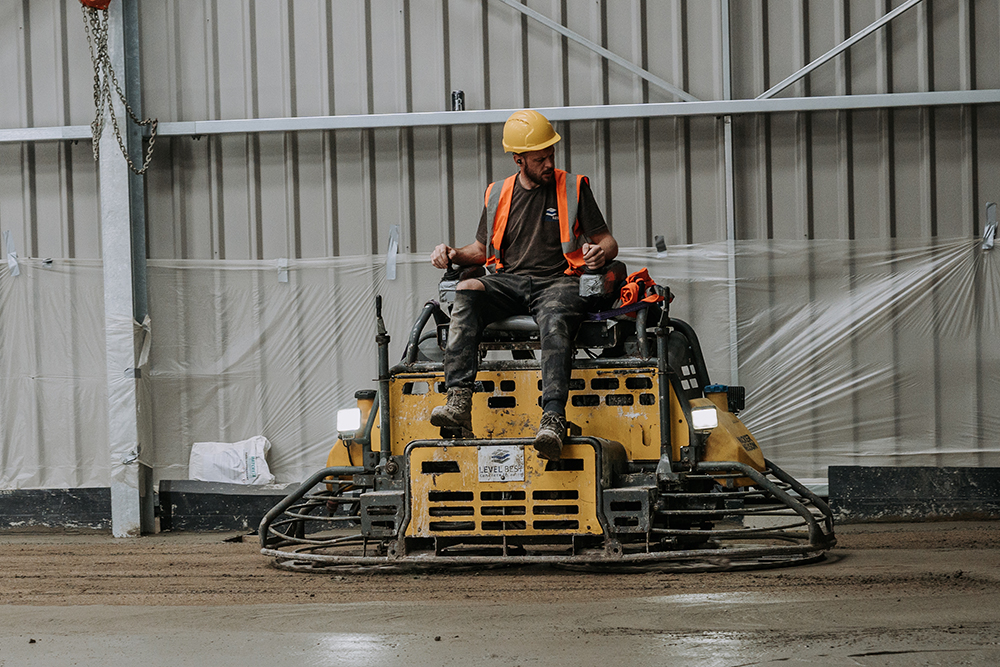
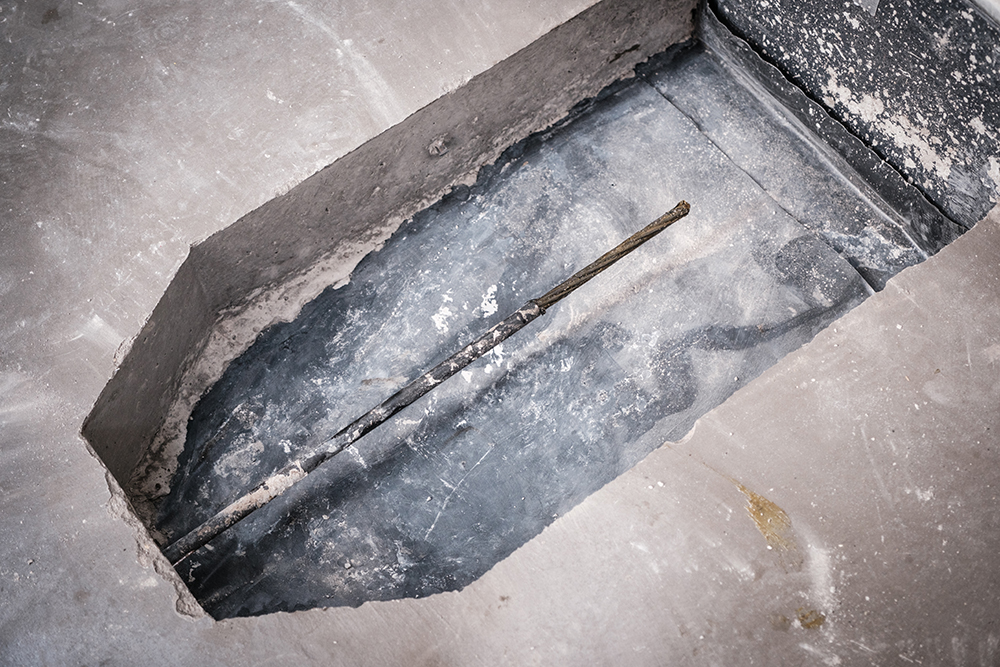
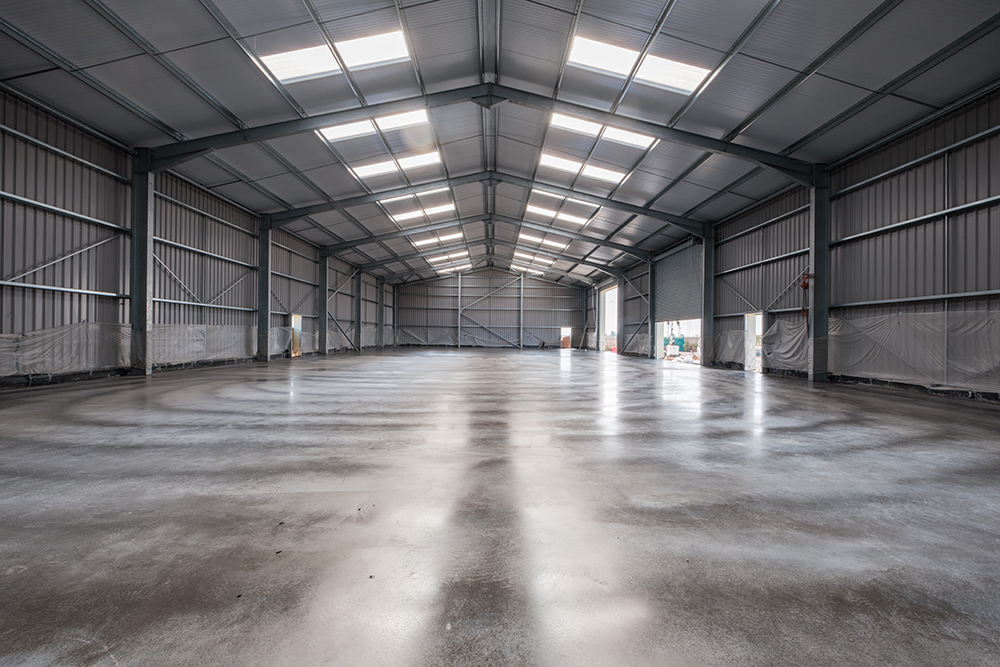
Step 3 - Stressing
Prior to the stressing operation, the post tensioning tendons were checked, and wedges were firmly installed into the anchors. As soon as the concrete achieved a compressive strength of 10MPa, 25% of the ultimate stress was applied. Once the compressive strength reached 25MPa, the final design stress was applied to the tendons. Initial stressing was done on day two after casting, final stressing a day later. The protruding strands were cut, and the stressing pockets then filled with steel fibre reinforced concrete. Depending on the concrete strength maturity in the first days from casting, initial and final stressing can be done faster.
Latest Projects
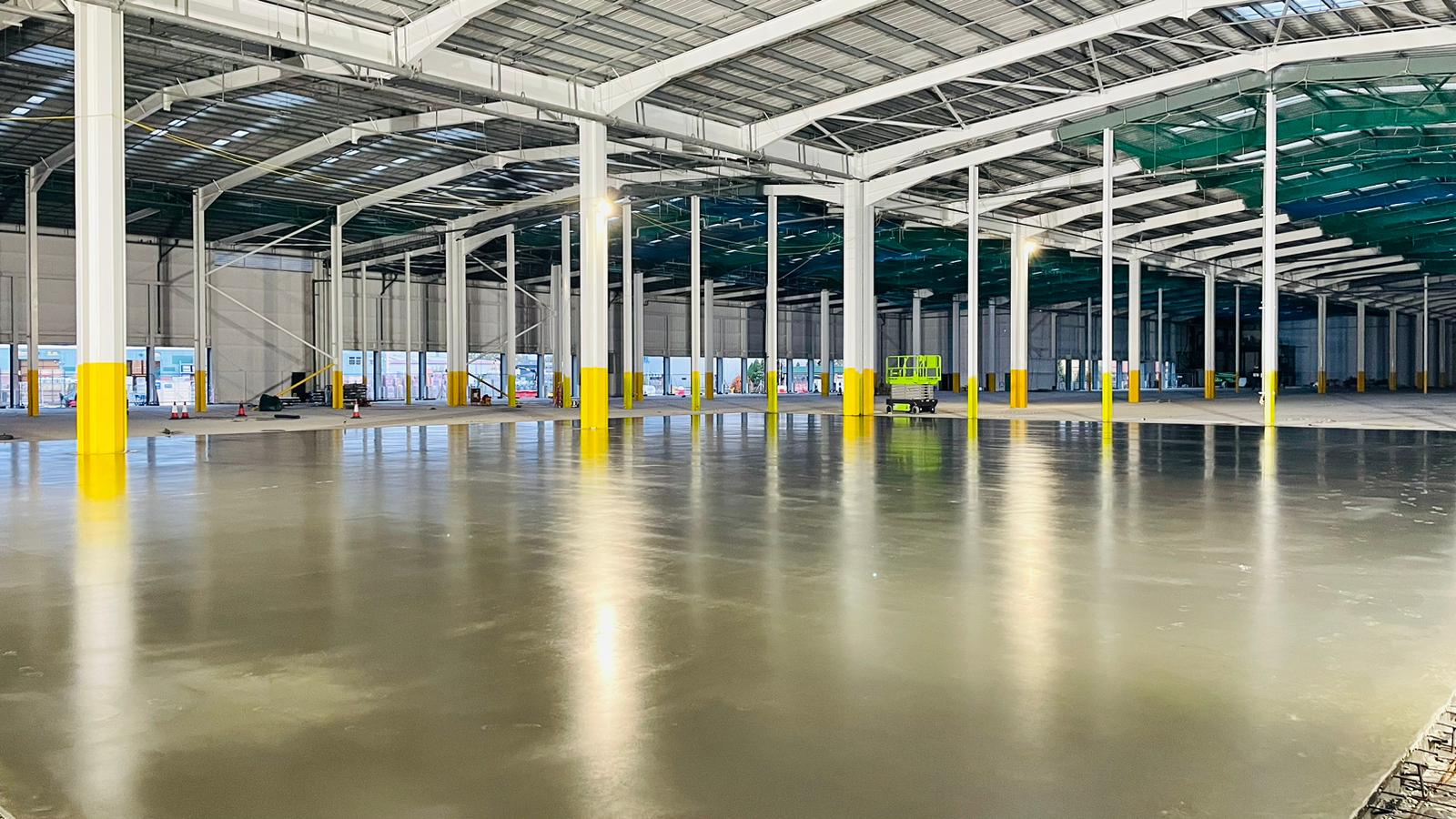
Industrial concrete flooring overlay in Long Eaton, Derbyshire
Level Best Concrete Flooring have been involved in a complex project in Long Eaton near Nottingham in Derbyshire involving the construction of 5,500 square metres of industrial concrete flooring as part of a major dilapidation project. Works commenced with the … Read More
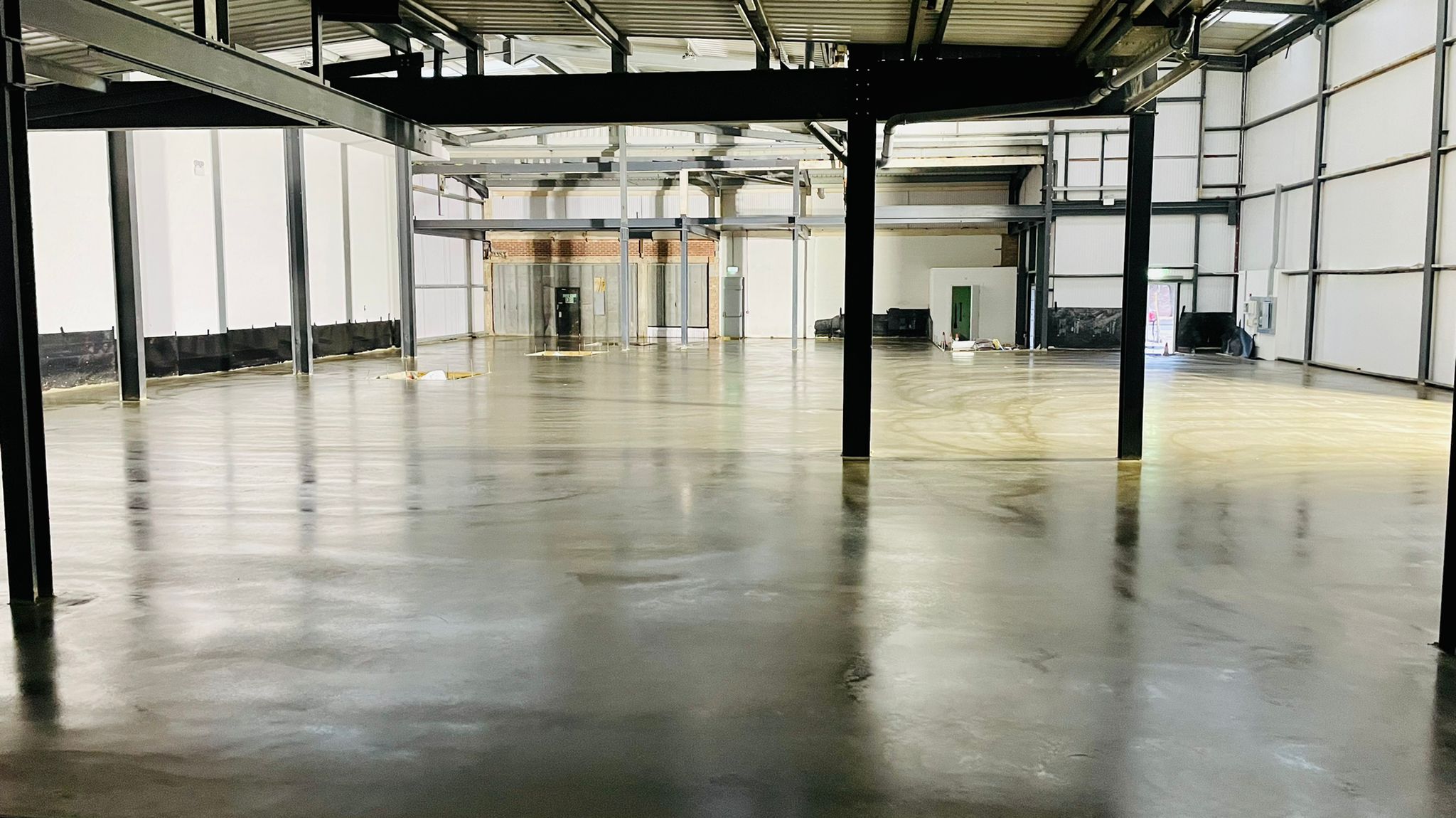
Bespoke commercial concrete flooring in Leamington Spa, Warwickshire
Industrial concrete flooring specialists, Level Best Concrete Flooring, have completed another medium-sized retro-fit bespoke industrial/commercial project on behalf of a private client and industrial landlord in the heart of central England in Leamington Spa, Warwickshire. Level Best worked closely with … Read More

Level Best Concrete Flooring has recently completed an overlay concrete floor slab in Didcot, Oxfordshire
Level Best Concrete Flooring has recently completed an overlay concrete floor slab in Didcot, Oxfordshire. The new floor slab was bonded to the old floor using a high strength bonding agent with extra strong capabilities to ensure the client doesn’t … Read More
Kind words from our Clients
Contact Level Best Concrete Flooring
We cover every aspect of Industrial Concrete Flooring repairs, installation and maintenance through the United Kingdom, and pride ourselves on tendering, designing and building the very best solution to suit your requirements.
You’re not going to hit a ridiculously long phone menu when you call us. Your email isn’t going in the the inbox abyss, never to be seen or heard from again. At Level Best, we provide the exceptional services we’d want to experience ourselves.
- Office Number : 01405 819199
- Out of Hours: 07539 360140
- enquiries@levelbestconcreteflooring.co.uk